“一台高效的绞线机,如何从零开始实现精密绞合?”——对于电线电缆、金属加工行业的从业者而言,这个问题直接关系到生产效率和产品质量。随着工业自动化需求的提升,掌握绞线机的制作原理不仅能降低设备采购成本,更能根据生产需求定制专属解决方案。本文将从结构设计、*关键部件选型*及*组装调试*三个维度,详解绞线机的制作全流程。
一、绞线机的核心功能与结构解析
绞线机的核心任务是将多根金属线或绝缘导线按预设的绞距和方向进行规则缠绕,形成具有抗拉伸、抗干扰特性的复合线缆。放线系统、绞合机构、牵引装置、收线系统四大模块构成了设备的基础框架。
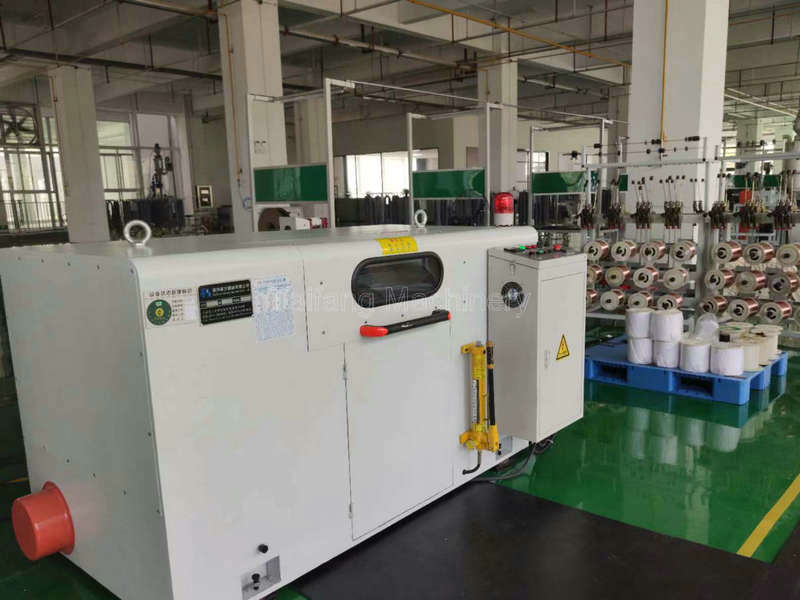
- 放线系统设计要点
采用*立式放线架*可有效避免线材缠绕,每个放线单元需配备独立张力控制器。建议选用带电磁制动器的放线盘,通过PID算法实现张力动态平衡。实验数据显示,张力波动控制在±5%以内时,绞合均匀度提升30%以上。
- 绞合头的机械创新
传统齿轮传动易产生振动噪音,而*行星轮系+伺服电机驱动*的组合方案能实现无级调速,绞距精度可达±0.1mm。关键部件建议使用42CrMo合金钢经渗氮处理,表面硬度HRC58-62,确保长期运转的耐磨性。
二、从零开始组装绞线机的关键步骤
(1)框架搭建与材料选择
主体框架推荐采用Q235B方钢焊接结构,重点加强绞合区域的支撑刚度。实测表明,当框架固有频率超过设备工作频率1.5倍时,可消除90%以上的共振风险。
(2)动力系统的匹配计算
根据绞合线径和转速需求,主电机功率可参考公式:
P= (T×n)/9550×η
(T为扭矩/N·m,n为转速/rpm,η取0.85-0.9)
例如处理Φ2mm铜线的设备,选用5.5kW伺服电机搭配1:30减速机,即可满足300rpm的稳定输出。
(3)核心部件的精准装配
- 绞合模具:锥形导模的入口角建议控制在12°-15°,过大会增加摩擦力,过小则影响绞合紧密度
- 导线轮组:采用陶瓷涂层导轮可减少线材表面划伤,安装时需保证各导轮轴线平行度≤0.02mm
- 计米装置:高精度光电编码器的应用,使长度误差控制在0.1%以内
三、提升设备性能的三大技术创新
- 智能张力控制系统
通过加装*薄膜压力传感器*和PLC闭环控制,能实时监测各放线单元的张力变化。某厂商测试数据显示,该系统使废品率从1.2%降至0.3%。
- 模块化设计理念
将绞合头设计为快拆式结构,配合不同规格的模具组件,可在15分钟内完成Φ0.5mm到Φ6mm线径的切换,设备利用率提升40%。
- 振动抑制方案
在轴承座与机架间加装聚氨酯减震垫,同时采用动平衡等级G2.5的主轴,使设备运行噪音从85dB(A)降至72dB(A)。
四、调试优化与常见问题对策
首次试机应遵循”低速空载→带载测试→满负荷运行”的渐进原则。重点关注:
- 绞合节距偏差:检查编码器信号采集是否受电磁干扰
- 线材表面擦伤:调整导轮组对中精度,必要时增加石墨润滑装置
- 收线不整齐:优化排线器的往复运动算法,建议采用模糊PID控制
某线缆生产企业通过优化退扭装置的角度,成功将7股绞线的断线率从8次/班降至1次/班。这印证了细节调整对整体性能的关键影响。
特别提示:制作过程中需严格遵守GB/T 23144-2008《绞线机》标准,电气部件必须符合IP54防护等级。定期使用频闪仪检测绞合节距,建立设备维护档案记录轴承温度、振动值等关键参数。