裁线机作为线材加工领域的核心设备,其稳定性直接影响线束生产效率和产品质量。然而,在日常使用中,操作人员常会遇到裁切精度偏移、设备卡顿甚至突发停机等问题。本文聚焦裁线机十大高频故障场景,结合行业维修数据与工程师实战经验,为您提供*系统化解决方案*与预防性维护策略。
一、裁线精度失控:从毫米误差到批量报废
当设备出现*线长不一致*或*切口毛刺*时,优先排查三点核心要素:
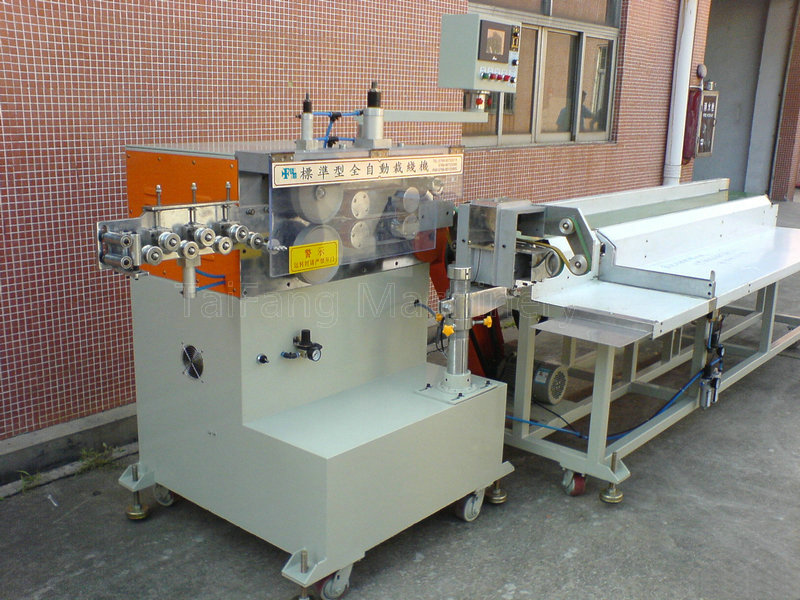
- 传感器灵敏度异常:光电感应器积尘或位置偏移会导致检测误差,需用无尘布清洁感应窗口并重新校准位置;
- 参数设置与线材特性不匹配:例如直径1.5mm的硅胶线与0.8mm的PVC线需调整不同的夹持压力值;
- 刀片磨损周期超限:双刃滚刀连续裁切30万次后,刃口圆角超过0.05mm即需更换(可通过投影仪测量确认)。
二、设备异响与振动:隐藏在噪音中的危险信号
若裁线机运行时伴随*金属摩擦声*或不规则震动,需按以下流程诊断:
- 传动系统检查:拆解齿轮箱观察润滑油是否变质(正常应为透明淡黄色),同步检查皮带张紧度(用张力计测量需达到80-100N);
- 轴承寿命预警:高速轴承工作8000小时后磨损概率激增,可通过频谱分析仪检测振动频率是否超过ISO 10816标准值;
- 结构件松动排查:使用扭矩扳手复紧X/Y轴导轨固定螺栓至出厂设定值(通常为25-30N·m)。
三、送线机构卡滞:80%故障源于这三个环节
线材输送不畅往往导致生产中断,重点检查送线轮组、矫直模块与张力控制系统:
- 送线轮沟槽磨损:当V型槽深度减少0.3mm时(用游标卡尺测量),需更换整套送线轮;
- 矫直辊调节失衡:采用五点矫直法时,各辊间隙应遵循”前松后紧”原则,建议用塞尺调整至线径的1.2倍;
- 张力器参数漂移:磁粉制动器电流值波动超过±5%时,需用万用表检测控制板输出信号并重置PID参数。
四、电气系统故障:精准定位的三大突破口
面对*PLC报警*或驱动器异常,可按照信号追踪法快速定位:
- IO模块诊断:通过编程器强制输出测试,若电磁阀响应延迟超过0.5秒,检查24V电源稳定性;
- 伺服系统排查:记录Err-09(过载报警)时的实际负载率,超过额定值85%需检查机械传动阻力;
- 人机界面死机:升级HMI固件至最新版本(如威纶通MT8102iE需升级至V4.0.5以上),并定期清理缓存文件。
五、预防性维护黄金法则:让裁线机效能提升30%
建立*四级保养体系*可显著降低故障率:
- 日常点检(每班次):清洁刀模残留铜屑(使用磁性拾取器),检查气压值稳定在0.55-0.6MPa;
- 周度保养:给直线导轨加注锂基润滑脂(NLGI 2级),校验裁切长度误差(用标准量块测量应≤±0.1mm);
- 月度维护:更换过滤器滤芯(精度5μm),全面检查接线端子紧固状态;
- 年度大修:更换全部O型密封圈,对伺服电机进行绝缘电阻测试(需≥50MΩ)。
六、特殊场景应对方案:突破行业痛点
针对多芯屏蔽线、*高温硅胶线*等特殊材料,建议采用定制化配置:
- 防静电设计:加装离子风棒(风速≥8m/s)消除线皮切割静电;
- 恒温系统:在刀座部位集成加热模块(控温精度±2℃),防止低温环境下的硅胶线粘刀;
- 视觉辅助系统:安装500万像素工业相机,实现线序颜色AI识别(识别速度≤0.3秒/次)。
通过掌握这些关键技术节点,企业可将裁线机综合效率(OEE)从行业平均的65%提升至82%以上。定期开展设备状态分析(建议使用MTBF计算方法),建立故障数据库,逐步实现从被动维修到预测性维护的战略转型。