在汽车、电子、通信等行业中,线束是连接设备与系统的“神经脉络”,其质量直接影响产品的稳定性和安全性。而作为线束制造的核心环节,绞线工艺的规范操作直接决定了线缆的导电性、抗干扰性及耐用性。然而,许多线束厂在实际操作中因流程不规范导致产品良率下降,甚至引发安全隐患。本文将围绕线束厂绞线的正确方法,从设备选择到操作细节,系统梳理7个关键步骤,助您实现高效、高质的生产目标。
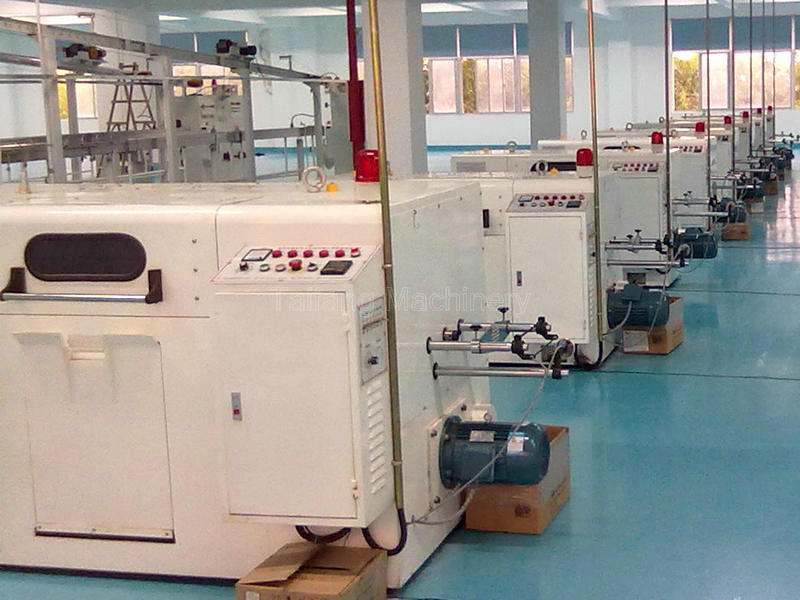
一、绞线前的准备工作:设备与材料的科学匹配
- 设备选型与调试
绞线机的性能直接影响绞合效果。需根据线材直径、绞合节距等参数选择扭矩稳定、转速可调的机型。例如,细线(0.1-0.5mm²)适合使用高速精密绞线机,而粗线(10mm²以上)需搭配大功率设备。调试时,需重点检查绞合模具的同心度,避免因偏移导致线芯磨损。
- 材料预处理
*导体退扭*是绞线前的必要步骤。单丝若存在内应力,绞合后易回弹变形。可通过退扭机或自然悬挂方式释放应力。同时,检查绝缘层是否均匀,避免因厚度不均导致绞合后外径波动。
二、绞线操作的核心步骤
- 绞合节距的精准控制
绞合节距(即单线螺旋一周的轴向长度)是影响线缆柔韧性与电阻的关键参数。经验公式为:节距=绞合外径×15~25倍。例如,外径2mm的线束,节距宜控制在30-50mm。实际操作中需通过试绞调整至最佳值,并用卡尺实时监测。
- 张力均衡与同步放线
多根单线绞合时,若张力不均会导致线芯松散或断裂。建议使用主动放线装置,通过传感器动态调节各线轴的张力。例如,某日企生产线通过闭环控制系统将张力误差控制在±5%以内,显著提升了绞线紧密度。
- 绞向与层数的合理设计
*绞向*分为左向(S绞)和右向(Z绞),多层绞线需交替使用以抵消扭矩。例如,内层采用S绞,外层则用Z绞,可减少线束扭曲。对于屏蔽层或高柔性需求场景,可增加绞合层数至3-4层。
三、绞线后的质量检验与问题处理
- 关键指标的检测方法
- 电阻测试:使用微欧计测量单位长度电阻,偏差超过5%需排查导体纯度或绞合紧密度问题。
- 外观检查:通过放大镜观察表面是否有毛刺、压痕,并用千分尺检测绞合外径是否符合公差(通常为±0.02mm)。
- 抗拉试验:模拟实际使用场景,对绞线施加1.5倍额定拉力,持续1分钟后检查是否断裂或变形。
- 常见问题与解决方案
- 松散绞合:多因节距过大或张力不足,可缩短节距并校准放线张力。
- 跳股或断线:检查导轮是否卡顿,或单线表面存在划伤。
- 截面不圆整:需更换绞合模具或调整绞合角度至30°-45°。
四、工艺优化:从经验到数据的升级
随着智能制造的发展,*基于大数据的绞线工艺优化*成为趋势。例如,某德系汽车线束厂通过采集设备振动、温度、转速等数据,建立AI模型预测绞合缺陷,使不良率从1.2%降至0.3%。此外,引入MES系统(制造执行系统)可实时监控生产参数,自动生成工艺改进建议,大幅提升标准化水平。
通过上述7个步骤的系统实施,线束厂不仅能提升绞线效率,更能确保线缆在复杂环境中的可靠性与寿命。从设备调试到工艺创新,每一步的精细化管控都是赢得市场竞争力的基石。