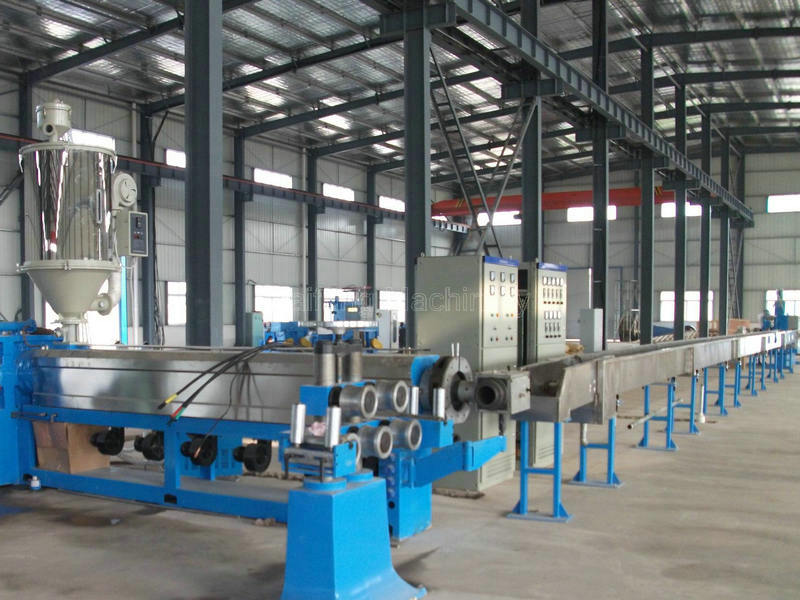
在当今工业制造领域,聚碳酸酯(PC)由于其优越的透明性、抗冲击性和加工性能,广泛应用于汽车制造、建筑材料、电子产品等多个领域。而PC挤出机作为生产过程中不可或缺的设备,通过精确控制温度和压力,将PC颗粒加工成各种规格的型材产品。了解PC挤出机的生产工艺流程图,对于提高产品质量、优化生产效率具有重要意义。
PC挤出机的生产工艺流程可以分为以下几个阶段:
- 原料准备:选择合适规格的PC颗粒作为原材料。这些颗粒通常需要经过干燥处理以除去水分,防止在挤出过程中发生降解或产生气泡。
- 加料:将干燥后的PC颗粒通过加料口送入挤出机的料斗中。现代挤出机通常配备自动上料系统,以确保连续稳定的供料。
- 挤压成型:PC颗粒在挤出机内被加热至熔点以上的温度,并在螺杆的旋转推动下向前移动,逐渐塑化形成均匀的熔融状态。这一过程对温度和速度的控制至关重要,直接影响到最终产品的质量和性能。
- 模具成型:熔融的PC材料从挤出机的模头中挤出,并通过特定的模具形状冷却固化,形成所需的型材截面。模具的设计和精度决定了产品的形状和尺寸精度。
- 定型与冷却:新挤出的产品需要通过定型装置来确保尺寸稳定,随后进入冷却水槽或风冷系统进行快速降温,以提高制品的机械强度和尺寸稳定性。
- 切割与检验:冷却后的产品根据需求长度进行切割,并进行质量检验,包括尺寸、外观及物理性能等指标的检查,以保证产品质量符合标准。
- 包装与储存:合格的PC型材将被适当包装,并储存于干燥通风的环境中,避免受潮或阳光直射造成质量下降。
通过对PC挤出机生产工艺流程的了解,可以看出每个环节都至关重要,不仅影响产品质量,也关系到生产成本和效率。因此,企业在操作过程中需严格控制各个环节,确保整个生产线的顺畅运行,从而在竞争激烈的市场中占据有利地位。