在环保建材需求激增的今天,聚丙烯(PP)管材因其耐腐蚀、轻量化、环保无毒等特性,成为给排水、化工输送、农业灌溉等领域的首选材料。而作为PP管材生产的“心脏设备”,PP管挤出机的技术水平直接决定了管材的质量与生产效率。如何选择一台性能优越的挤出机?其核心技术有哪些创新突破?本文将深入解析这一关键设备的运作原理、技术优势及市场应用价值。
一、PP管挤出机的工作原理与核心结构
PP管挤出机通过高温熔融、加压挤出的方式,将聚丙烯原料塑化成连续管材。其核心流程包括:
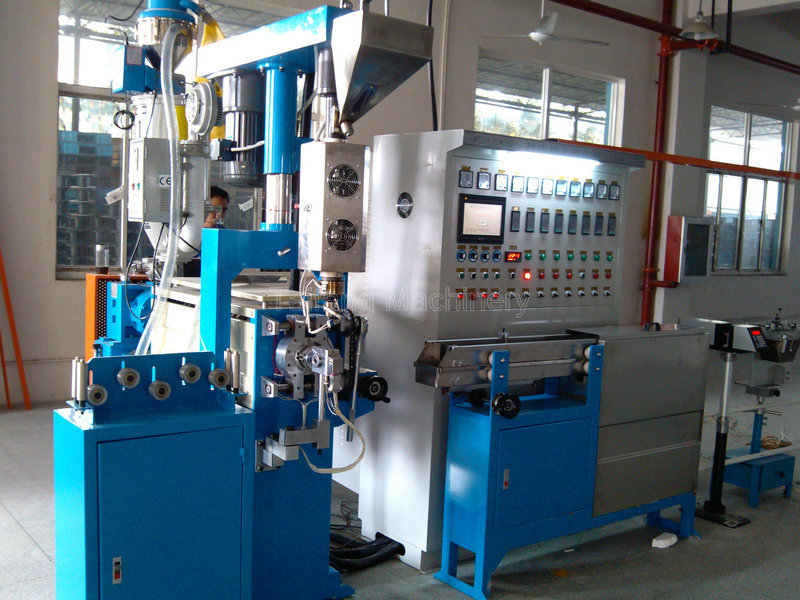
- 原料预处理:PP颗粒经干燥系统去除水分,确保熔融过程无气泡;
- 熔融挤出:螺杆将原料推送至加热筒,在180-240℃高温下熔融;
- 模具定型:熔体通过环形模具形成管状结构,经真空定径箱冷却定型;
- 牵引切割:管材由牵引机匀速拉出,按设定长度切割。
*关键组件*中,螺杆设计直接影响塑化效率。现代挤出机多采用渐变式或屏障型螺杆,通过分段压缩和混炼功能,实现原料均匀熔融。此外,双阶真空排气系统可有效排除熔体中的挥发性物质,避免管材内部缺陷。
二、PP管挤出机的四大技术优势
- 高产能与节能性
采用伺服电机驱动和智能温控系统,能耗降低20%-30%,单机日产量可达3-5吨。例如,某品牌挤出机通过优化螺杆长径比(32:1),实现原料塑化时间缩短15%。
- 精准的尺寸控制
配备激光测径仪与闭环反馈系统,管材外径误差可控制在±0.1mm以内,满足DN20-DN1200多种规格需求。
- 材料适应性广
通过更换模具和调整工艺参数,可兼容PP-R、PP-H、PP-B等多种聚丙烯原料,甚至添加玻纤增强材料生产高压管材。
- 智能化操作
人机界面(HMI)集成温度、压力、速度等参数监控,支持一键启动和故障诊断,降低人工干预需求。
三、如何选择适合的PP管挤出机?
选购设备时需结合生产需求与投资预算,重点关注以下指标:
- 螺杆直径与长径比:直径越大,产能越高;长径比建议不低于28:1以确保塑化效果;
- 驱动功率:一般按产能1.5-2倍配置,避免超负荷运行;
- 控制系统:优先选择配备PLC或物联网模块的设备,便于数据追溯与远程管理;
- 品牌与服务:选择拥有成熟案例的厂商,确保售后技术支持。
案例参考:某水务工程企业采购一台Φ90mm螺杆挤出机,配合双层共挤模具,成功生产出兼具抗紫外线外层与抗菌内层的双壁PP管,产品寿命提升30%。
四、行业趋势:绿色制造与智能化升级
随着“双碳”目标推进,PP管挤出机正朝着两大方向革新:
- 节能降耗技术:如电磁感应加热替代传统电阻加热,热效率提升至85%以上;
- 数字孪生应用:通过虚拟仿真优化工艺参数,减少试机损耗。
值得关注的是,部分厂商已推出模块化设计的挤出机,用户可自由组合喂料、排气、造粒单元,快速切换管材、板材等不同生产线,显著提高设备利用率。
五、维护保养:延长设备寿命的关键
为确保PP管挤出机长期稳定运行,需建立科学的维护制度:
- 每日检查:清理模具残留物,润滑传动部件;
- 月度保养:校准温度传感器,检查加热圈绝缘性能;
- 年度大修:更换磨损螺杆,检测电机轴承状态。
常见问题预警:若管材表面出现波纹或气泡,可能是螺杆转速过高或温度控制失衡,需及时调整工艺参数。
通过以上分析可见,PP管挤出机不仅是聚丙烯管材生产的核心装备,更是企业提升竞争力、响应市场需求的战略投资。从原料到成品,从硬件到软件,其技术创新与智能化升级将持续推动管材行业向高效、环保、高附加值方向迈进。