“生产线又停机了?这次是挤出机螺杆卡死还是料筒温度异常?” 在塑料制品行业,这样的问题几乎每天都会困扰着技术人员。据统计,挤出机故障导致的停机时间占生产线总停机时间的35%以上,直接影响企业产能和利润。本文将针对*塑料挤出机生产线*的核心痛点,系统梳理十大高频故障现象及其专业解决方案,助您快速定位问题、恢复生产。
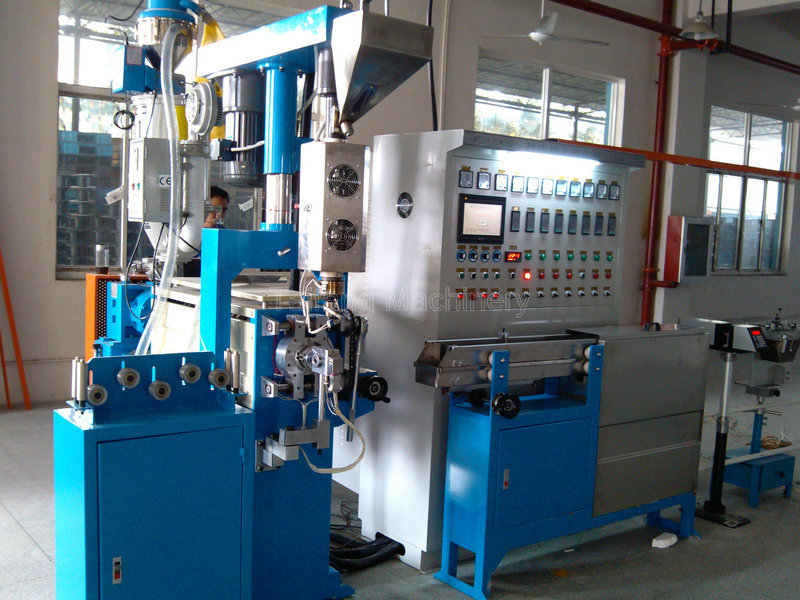
一、原料处理类故障
- 物料塑化不良
典型现象:制品表面粗糙、出现气泡或晶点,*熔体压力表*显示数值波动剧烈。
根本原因:①原料含水率超标(如PET含水量>0.02%);②螺杆压缩段设计不合理;③加热温区设定偏差超过±5℃。
解决方案:优先使用双阶式除湿干燥机,确保原料含水率≤0.005%;对于PP/PE材料,建议采用渐变型螺杆并检查三区(熔融段)温度是否达到200-230℃。
- 喂料口架桥
突发状况:进料斗物料堆积成拱形,导致螺杆空转。这种情况在加工*再生料*时发生率提升40%。
应急处理:立即停机并采用铜棒轻敲料斗侧壁,同时检查搅拌器转速是否低于20r/min。长期预防需在料斗加装破拱装置或改用强制喂料系统。
二、设备核心部件故障
- 螺杆异常磨损
当*熔体泵出口压力*持续高于25MPa时,可能预示螺杆/料筒间隙超过0.3mm标准值。某ABS生产线案例显示,磨损的螺杆会使能耗增加18%。
维护要点:每月测量螺杆外径,使用硬质合金喷涂修复;对于加工玻纤增强材料,务必选用双金属料筒(表面硬度HRC58以上)。
- 加热圈失效连锁反应
某PVC管材生产企业曾因单个加热圈断路导致整机温控误差达±15℃,引发焦料堵塞模头。
诊断技巧:使用红外测温枪比对设定值与实际温度,温差超过±3℃应立即检查加热圈电阻(正常值18-22Ω)。推荐采用陶瓷加热圈替换传统云母片式结构。
三、工艺控制类故障
- 熔体破裂(Melt Fracture)
特征表现:制品表面呈现周期性鲨鱼皮纹路,常见于HDPE高速挤出(线速度>50m/min)。
工艺优化:将口模温度提高10-15℃,同时添加0.5%-1%的氟弹性体加工助剂。实验证明,此法可使临界挤出速度提升至80m/min。
- 真空排气口冒料
当加工含水量>0.03%的PA66时,若二级排气段真空度<-0.08MPa,极易发生熔体喷溅。
关键技术:采用两级真空系统(前级-0.05MPa,后级-0.09MPa),并在排气孔上方安装熔体过滤器(目数80-100目)。
四、传动系统故障
- 主电机过载跳闸
在更换模具后突然出现的过载报警,往往与扭矩保护值设定不当有关。计算公式:额定扭矩=9550×电机功率(kW)/螺杆转速(r/min)。
调试规范:新模具试机时,应将扭矩限定在额定值的70%-80%,逐步调整至工艺稳定状态。
- 减速箱异常振动
频谱分析显示,当振动加速度值>7.1m/s²时,轴承故障概率达92%。某品牌减速箱维修数据显示,60%的故障源于润滑油颗粒污染(NAS等级超过8级)。
保养制度:严格执行2000小时换油周期,选用ISO VG220重负荷齿轮油,每月检测油液清洁度。
五、辅助系统故障
- 水循环系统结垢
预警信号:水温差>5℃(正常值2-3℃),年结垢1mm可使换热效率下降15%。
创新方案:在闭式冷却塔添加电子除垢仪,配合季度性化学清洗(柠檬酸浓度3%-5%),可使模具冷却速率提升22%。
- 切粒机刀片崩刃
当PET切粒出现连粒时,往往误判为水温问题,实则80%案例源于动刀与定刀间隙偏离0.03-0.05mm标准值。
精密调整:使用塞尺配合激光对中仪,确保四把刀片间隙偏差≤±0.01mm。采用粉末冶金钢刀片可延长使用寿命至3000小时以上。
通过上述系统化故障树分析可见,*塑料挤出机*的高效运行需要原料预处理、设备维护、工艺优化三管齐下。建议企业建立《关键参数监测台账》,对螺杆转速、熔体压力等12项核心指标实施动态监控,将非计划停机率控制在3%以内。